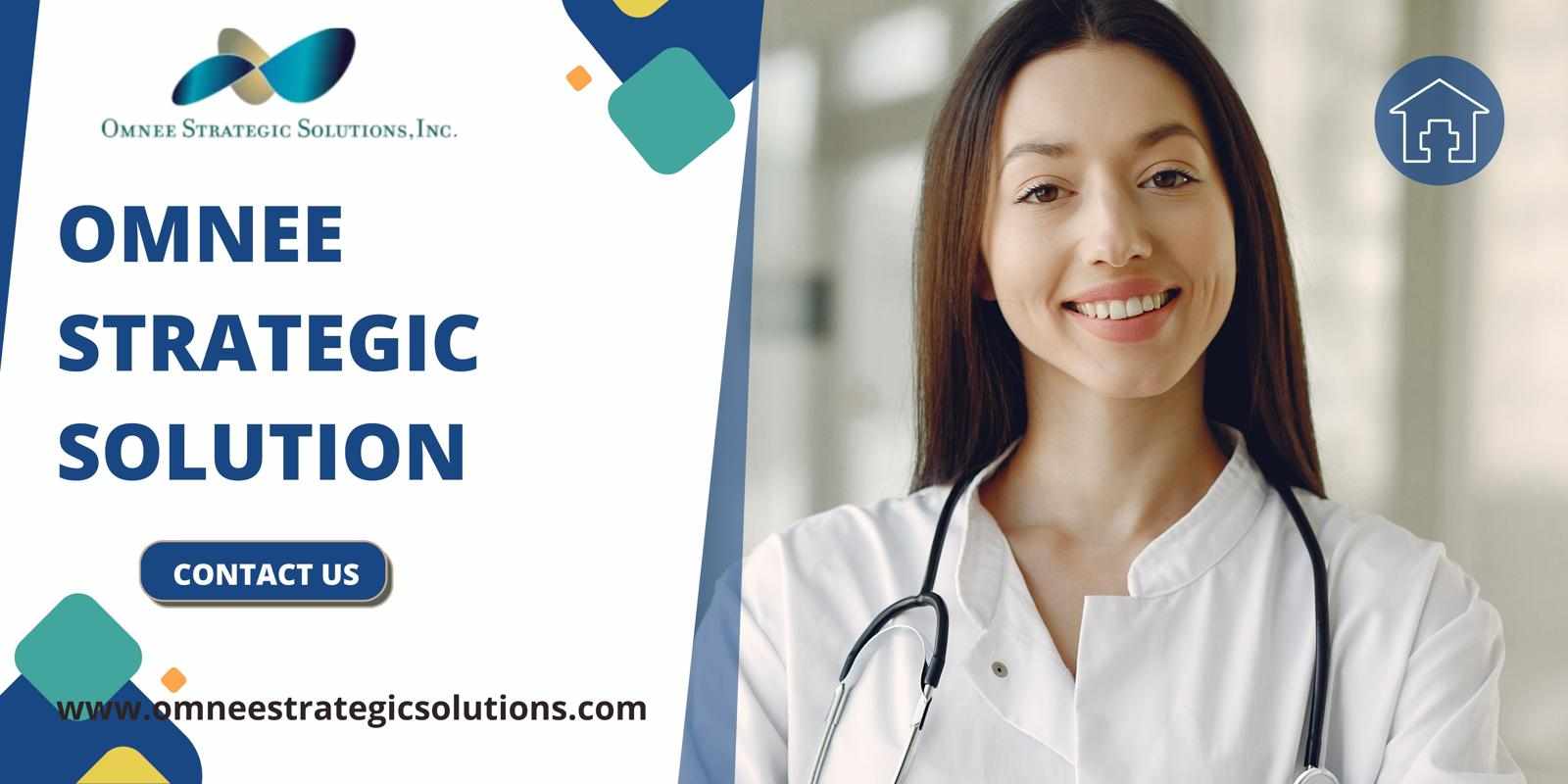
The medical device industry is highly regulated due to the critical role that these devices play in healthcare. Ensuring product quality, safety, and regulatory compliance is crucial, and a well-established Medical Device Quality Management System (QMS) is central to achieving this. A QMS helps organizations consistently meet regulatory requirements, improve product quality, and ensure patient safety. In this blog, we’ll explore the importance of having an effective QMS in the medical device industry, key components of a QMS, and the benefits it offers.
The Role of a Medical Device Quality Management System
A Medical Device Quality Management System is a framework of processes and procedures that manufacturers implement to ensure the safety, efficacy, and reliability of their medical devices. It covers all stages of the device lifecycle, from design and development to post-market surveillance. Regulatory bodies, such as the FDA and ISO, require medical device companies to have a robust QMS in place to ensure that devices are manufactured consistently and according to strict standards.
The importance of a QMS extends beyond regulatory compliance. A well-implemented QMS fosters continuous improvement and helps manufacturers detect and address defects early in the production process, thereby reducing the risk of product recalls or patient harm.
Key Components of a Medical Device QMS
Document Control: Maintaining accurate, up-to-date documentation is vital in a Medical Device Quality Management System. This includes everything from product specifications and design documents to risk management reports and manufacturing records. Document control ensures that all team members have access to the most current information, reducing the likelihood of errors.
Risk Management: A key aspect of any QMS is identifying and mitigating risks associated with medical devices. ISO 14971 is the international standard for risk management in the medical device industry. Through risk assessment processes, manufacturers can proactively address potential hazards before devices reach the market.
Supplier Quality Management: The quality of materials and components from suppliers has a direct impact on the finished medical device. Therefore, a QMS should include robust supplier evaluation and monitoring processes to ensure compliance with specifications.
Corrective and Preventive Actions (CAPA): CAPA processes are crucial for identifying non-conformances and implementing corrective measures to prevent recurrence. These processes ensure that manufacturers address quality issues swiftly and thoroughly.
Post-Market Surveillance: Once a device is released to the market, ongoing monitoring is essential to ensure it performs as intended. A Medical Device Quality Management System should include mechanisms for tracking adverse events, complaints, and product performance, enabling manufacturers to make necessary adjustments.
Benefits of a Medical Device QMS
Regulatory Compliance: Having a QMS in place is mandatory in most regions for regulatory approval. A well-documented Medical Device Quality Management System ensures compliance with standards such as ISO 13485, facilitating easier market access.
Improved Product Quality: By focusing on continuous improvement, a QMS enables manufacturers to consistently produce high-quality devices. It fosters a culture of quality throughout the organization, improving customer satisfaction.
Risk Reduction: Identifying and mitigating risks at every stage of the device lifecycle reduces the likelihood of product failures or recalls. This proactive approach helps protect patients and healthcare providers, while also safeguarding the company’s reputation.
Cost Savings: Early detection and correction of issues reduce the risk of expensive recalls and rework. A QMS enables manufacturers to address quality concerns before they escalate, saving time and resources.
Best Practices for Implementing a Medical Device QMS
To effectively implement a Medical Device Quality Management System, manufacturers should follow these best practices:
Engage Leadership: Top management should be actively involved in QMS implementation and maintenance. Their commitment to quality sets the tone for the entire organization.
Regular Training: Employees at all levels should receive ongoing training on QMS procedures and regulatory requirements. This ensures that everyone understands their role in maintaining product quality.
Internal Audits: Conducting regular internal audits helps identify areas for improvement and ensures the QMS remains compliant with regulatory standards.
Continuous Improvement: A QMS should be dynamic, evolving in response to new challenges and regulatory updates. Manufacturers should encourage a culture of continuous improvement to enhance product quality over time.
Conclusion
A Medical Device Quality Management System is essential for ensuring product quality, regulatory compliance, and patient safety. By establishing a robust QMS, manufacturers can improve product consistency, reduce risks, and foster a culture of continuous improvement. As the regulatory landscape for medical devices becomes increasingly stringent, having a well-functioning QMS is more critical than ever.
Write a comment ...